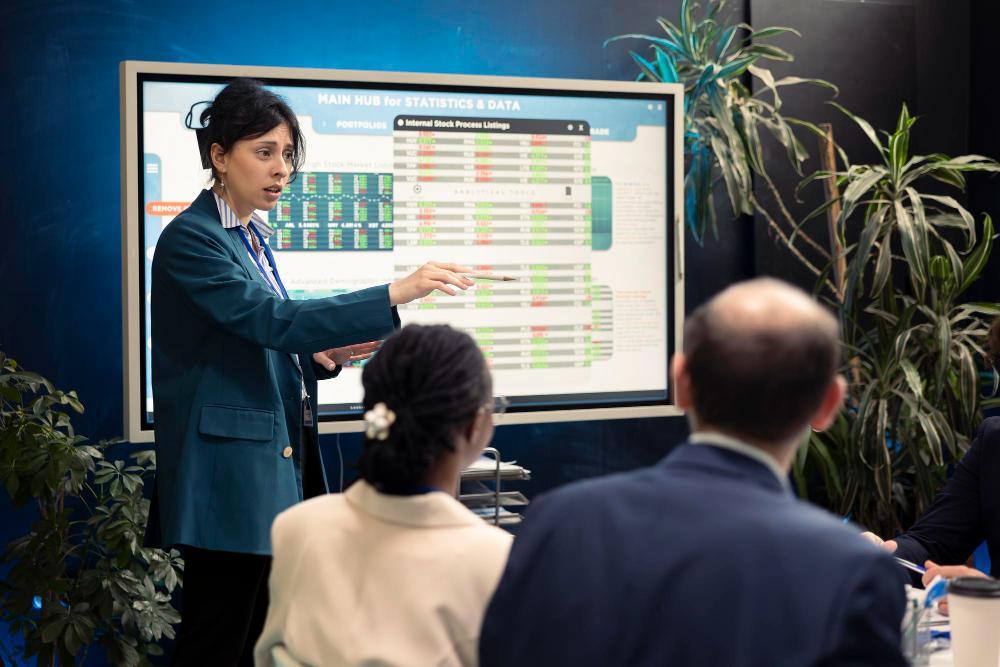
In today’s high-pressure, fast-paced business world, efficiency has evolved from a competitive edge into a matter of survival. Whether it’s cutting costs, improving quality, or reducing delays, organizations in 2025 are under constant pressure to optimize their operations. But in many cases, businesses are discovering that traditional approaches to problem-solving no longer deliver sustainable results.
This is where structured improvement methodologies like Lean Six Sigma continue to stand out—especially at the Black Belt level, which is increasingly being adopted by professionals leading complex, high-impact change initiatives. This article explores how Black Belt-certified professionals are tackling real operational bottlenecks across industries and why structured process training remains relevant in an era dominated by AI and digital transformation.
Why Traditional Problem-Solving Falls Short
Despite advances in technology and access to vast amounts of data, many companies still rely on fragmented or outdated approaches to improvement—quick fixes, anecdotal decisions, and siloed efforts. These often treat symptoms rather than root causes, which leads to recurring issues and inefficient use of time and resources.
By contrast, Lean Six Sigma offers a data-driven, root-cause-focused framework. Professionals trained at the Black Belt level are equipped to lead organizational change through methods like DMAIC (Define, Measure, Analyze, Improve, Control), stakeholder analysis, and robust project execution.
Common Bottlenecks and How Black Belts Address Them
Although Lean Six Sigma tools are flexible enough to apply across industries, several recurring challenges continue to surface in 2025, particularly in manufacturing, healthcare, logistics, and professional services.
Complex Process Inefficiencies
Even well-established companies often operate with inefficient workflows—burdened by legacy steps, unclear responsibilities, and slow approvals. These inefficiencies aren’t always obvious but can lead to massive time and cost losses.
Black Belt professionals are trained to map processes end-to-end, identify value-added versus non-value-added steps, and facilitate process redesign that cuts out redundancy while preserving quality.
High Defect Rates and Frequent Rework
Product or service quality issues can be devastating, damaging brand trust, increasing rework costs, and eroding margins. In sectors like pharmaceuticals or aviation, the stakes are even higher.
Using tools like statistical process control and cause-and-effect analysis, certified professionals identify hidden sources of variation and eliminate them, reducing error rates and improving consistency over time.
Misaligned Metrics and Disconnected KPIs
In many organizations, teams are tracking dozens of metrics, but few truly support strategic goals. Inconsistent KPIs across departments make it harder to measure performance or justify change initiatives.
Lean Six Sigma Black Belts often play a key role in streamlining metrics, aligning them with overarching goals, and ensuring that improvement efforts are measurable and meaningful.
The Shift Toward Data-Driven Decision Making
One of the major shifts organizations have undergone in recent years is the move from subjective decision-making toward data-backed problem solving. This transition, however, requires more than just access to dashboards—it demands the ability to interpret, question, and act on data meaningfully.
Black Belt professionals are trained to:
- Select relevant and reliable data sources
- Conduct statistical analysis using tools like Minitab or JMP
- Apply hypothesis testing to validate assumptions
- Present insights in a way that both technical and non-technical stakeholders can understand
This helps bridge the gap between data and decision, reducing guesswork and enabling more confident execution.
Case Snapshot: Logistics and Lead Time Reduction
A mid-sized logistics firm in the U.S. faced persistent delivery delays—on average, orders were running 3 to 5 days behind schedule. While customer service teams bore the brunt of complaints, the actual root causes spanned multiple functions, from route optimization software limitations to inefficient warehouse loading procedures.
With the help of a process improvement lead trained in Lean Six Sigma at the Black Belt level, the company applied DMAIC to reevaluate workflows, retrain staff, and implement predictive tools for delivery scheduling. Within six months, the average delay time dropped by 70%, resulting in improved client satisfaction and annual savings of over $300,000.
It’s this type of outcome—data-backed, cross-functional, and measurable—that continues to make structured problem-solving approaches highly valuable in modern operations.
Why In-House Capability Matters in 2025
Previously, many organizations hired external consultants to handle process improvement. But as remote teams, hybrid work environments, and tech integration have become the norm, the need for internal change leadership has grown.
Having employees equipped with structured process knowledge and improvement capability creates long-term value by:
- Enabling faster response to operational issues
- Supporting ongoing optimization rather than one-time fixes
- Reducing reliance on external expertise
- Promoting a culture of evidence-based thinking
For professionals aiming to gain such capabilities, earning a recognized credential like the Lean Six Sigma Black Belt certification offers a comprehensive framework for leading impactful change.
Supporting Broader Business Strategies
One of the reasons Lean Six Sigma remains relevant in 2025 is its compatibility with other key business strategies. Rather than replacing other methodologies, it complements and strengthens them:
- Agile Development: While Agile drives iterative progress, Lean Six Sigma ensures that improvements are validated with data and supported by sustainable processes.
- Digital Transformation: Certified professionals often help identify which steps are worth automating and ensure that digital tools are integrated into well-structured workflows.
- Customer Experience (CX): By reducing process errors, improving handoffs, and enhancing service consistency, CX metrics like Net Promoter Score (NPS) often improve organically.
This adaptability makes Lean Six Sigma a versatile asset across sectors, from SaaS companies to hospital systems and retail chains.
Career Value Beyond the Certification
From a career perspective, Black Belt-level training continues to open doors. Professionals with process improvement expertise are often promoted into leadership roles, trusted with cross-functional initiatives, and seen as problem-solvers across departments.
Common roles held by Black Belt certified individuals include:
- Continuous Improvement Manager
- Process Optimization Lead
- Business Transformation Consultant
- Quality Operations Manager
- Senior Analyst (Data, Supply Chain, or Operational Risk)
In many cases, professionals report significant salary increases and job mobility after certification, not just because of the credential, but because of the skillset it represents.
Choosing a Meaningful Certification Path
Not all certification programs are created equal. With growing interest in process improvement, many quick courses have flooded the market, offering “guaranteed passes” or minimal training. But impactful learning goes beyond passing an exam.
A meaningful Black Belt program should provide:
- Real-world projects with measurable outcomes
- Access to mentors or instructors
- Case-based learning, not just theory
- Long-term access to tools, templates, and frameworks
While there are several options available, the key is to choose a platform that treats certification as a professional development journey, not a checkbox.
Final Thoughts: Solving What Matters
In a world where change is constant, businesses can no longer afford to rely on reactive solutions. The ability to identify problems clearly, understand their root causes, and lead structured improvements is no longer a specialized skill — it’s an operational necessity.
For organizations, developing internal talent with process improvement expertise is an investment in resilience. And for professionals, mastering frameworks like Lean Six Sigma Black Belt is about more than career growth—it’s about becoming someone who can consistently create clarity and progress in complex systems.
And that’s a capability every business, team, and customer will value—no matter what the future holds.